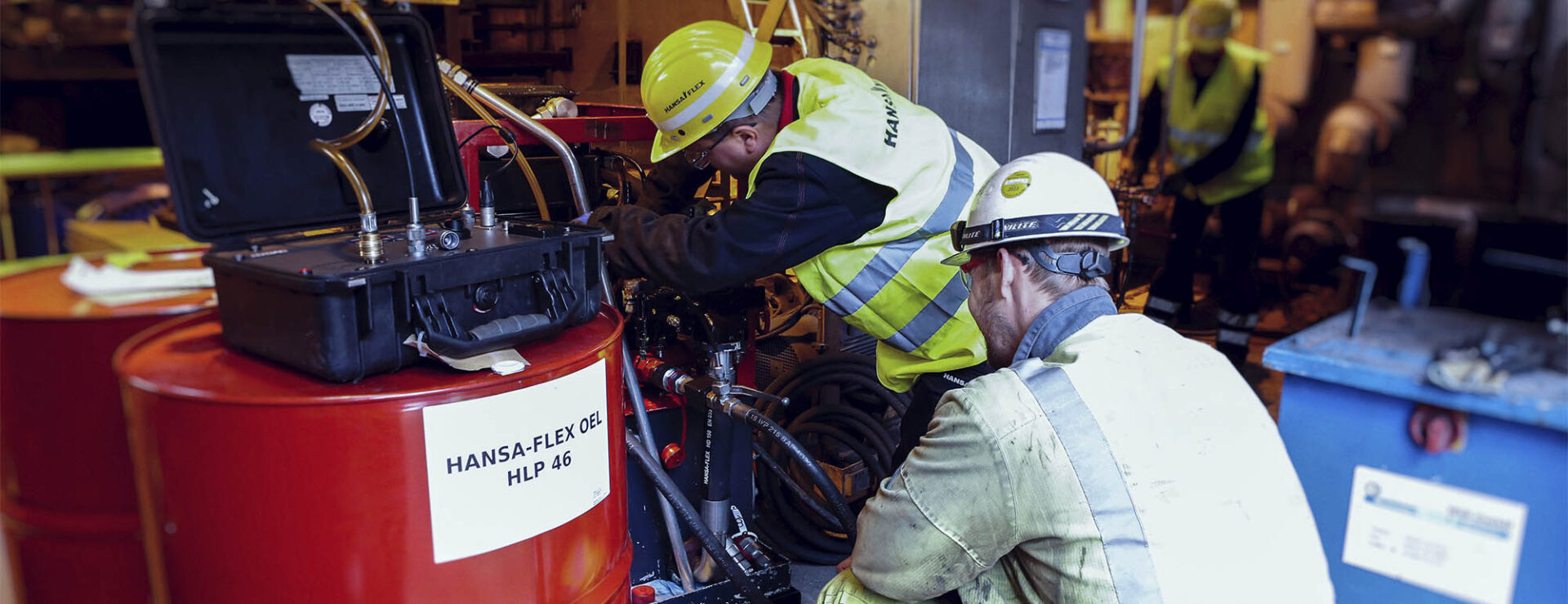
360° fluid management from hansa‑flex
Oil care is a key factor in ensuring trouble-free operation of hydraulic systems and plants. Contaminants in the fluid can have serious effects. From the analysis to the cleaning of the fluid right up to continuous condition monitoring during operation, HANSA‑FLEX fluid experts support you in all aspects of oil care for your systems and machines.
Comprehensive hydraulic oil care from the experts
With the benefit of know-how from HANSA‑FLEX fluid experts, you can avoid damage and downtimes
Comprehensive oil analysis
Read moreWhether mobile or stationary hydraulics: oil analysis forms the foundation for optimum oil care. Only if fluid-related problems are recognised in good time and measures to rectify them taken can expensive downtime and major replacements be prevented. For this reason, HANSA‑FLEX Fluid Service offers comprehensive oil analyses on site and in the laboratory.
Efficient oil cleaning
Read moreBy regularly filtering your oil, you can ensure that your hydraulic systems continue to function properly for longer. Solid and liquid contaminants cause abrasion, increase wear and promote corrosion. The HANSA‑FLEX fluid experts clean your oil professionally and find the perfect filter solutions for your field of application.
The 10 golden rules of oil care
Oil cleaning, detecting damage, system optimisation: Fluid care is complex, requiring a lot of knowledge and experience. What should you look for when dealing with hydraulic oil? Here is a list of the ten most important points: from the selection of a suitable hydraulic oil right up to using sensors to continuously monitor it.
The quality and cleanliness of the hydraulic oil used are crucial parameters for the operational reliability, service life and cost-effective operation of hydraulic systems. The advice of qualified fluid experts, lubricant manufacturers or dealers can prove very valuable in this respect.
To remove any foreign bodies that may have found their way into the system during installation, every hydraulic system must be flushed before first use and every subsequent bringing into use. In this way you can ensure that your system runs perfectly right from the start.
You have bought some fresh oil. Can you assume that it satisfies the cleanliness requirements? That could be a major mistake. It is not unusual for oil to be supplied in an unclean condition because oils are often not fine-mesh filtered during the production or filling process. Therefore, always ensure fresh oil is filtered before you put it into your system.
The mixing of different hydraulic fluids often leads to a dramatic worsening of their physical properties. You should always avoid mixing different oils because no combination of oils is ever 100 % problem-free. This applies to fluids with the same classification and to products with different viscosities.
Oil contamination with solids such as dust or particles of metal or seal material is one of the most frequent causes of damage and can lead to increased wear of the installed components. Contamination of oil with air or water can cause corrosion or cavitation. Suitable filtration solutions should be used and the system parameters optimised to avoid these damaging effects.
Have regular oil analyses performed in the laboratory or on site so that the oils used in your hydraulic systems achieve a consistently high quality standard. In this way, you will ensure a long service life for your systems and avoid expensive failures and long standstills.
You can use various filter systems, such as suction and return filters, to filter your oil. The filter elements should be changed at frequent intervals. Mobile filter systems, such as bypass filter systems, can also be hired from HANSA‑FLEX.
Too high an operating or ambient temperature reduces the performance of hydraulic oil. High temperatures can, among other things, lead to acid formation and high wear of the components. It is also worthwhile ensuring the tank contains the right volume of oil and using an oil cooler.
Are you installing a new hydraulic system? Pay attention to cleanliness to prevent foreign particles from entering the system. Before the system is brought into use, it should be thoroughly flushed clean.
Oil condition sensors help you to continuously monitor your hydraulic systems and drives. Your benefits: Malfunctions during operation can be quickly detected and the failure risks analysed.
Hydraulic oil contamination is the main cause of over 80 % of hydraulic system failures.
Author of “Liquid Gold: Oil filtration, the key to
Oil care – why it’s worth it
All the benefits at a glance
Everything works out better
Less damage from contamination, fewer failures and less downtime
Longer service life
Your machines and systems last much longer
Professional expertise
Our trained fluid specialists look after your oil and avoid damage to your systems
Know what’s wrong
Expert diagnoses find what’s wrong before it causes expensive damage
The 3 most important facts about the use of hydraulic oil
- Requirements
- Fluid management
- Monitoring
- Item 1
Everything oil must do
Hydraulic oil has to withstand high stresses. The pressure fluids standard DIN 51524 specifies the minimum requirements of hydraulic fluids. Other requirements:
- Shear stability (resistance to changes in viscosity)
- Filterability
- Low hygroscopicity (the tendency of an oil to absorb water), and resistance to thermal loads
- Item 1
More than just changing the oil
Fluid management involves more than just regular oil changes. Oil cleaning and analyses can help prevent failures and downtime. Where a hydraulic system has been carefully designed to achieve a specific performance, the requirements of the components used such as fluid and filtration solutions are particularly high. With professional advice from the fluid experts, you can lay the foundations for:
- Operational reliability
- Long service life
- Cost-effective operation
- Item 1
Fluid condition monitoring
Our experts continuously monitor the condition of the oil using oil condition sensors. This allows changes such as rising contamination levels to be recognised and rectified. The advantages:
- Detect malfunctions in systems while they are operating
- Quick rectification of damage
- Reduced risk of failure of equipment, machines and systems
- Continual optimisation of fluid management
Damage detection and fluid-related system optimisation
In the event of damage, the experienced HANSA‑FLEX fluid and hydraulics specialists perform an analysis on site. They quickly determine the reasons for the failure and provide extensive assistance with the implementation of all the measures required to rectify the damage. The experts also devise an action plan for your fluid management, so that oil-related system failures become a thing of the past.
Everything about clean hydraulic oil in a nutshell
Hydraulic fluid is an important system component and crucially significant to the design, operation and maintenance of hydraulic equipment. You can find everything you need to know about the undervalued component hydraulic oil in our brochure.
Something that may also interest you
Fluid management
Oil care is a key factor in ensuring trouble-free operation of hydraulic systems and plants. Contaminants in the fluid can…
Find out moreMobile rapid hydraulic service
When hydraulic components fail unexpectedly, you have to act fast. With 180 vehicles across Germany, our mobile Rapid Hydraulic Service…
Find out moreAssembly and installation
Our excellently trained service technicians carry out assembly and installation work on hydraulic systems. Irrespective of whether the work involves…
Find out more