Sweet fruits for beckers bester
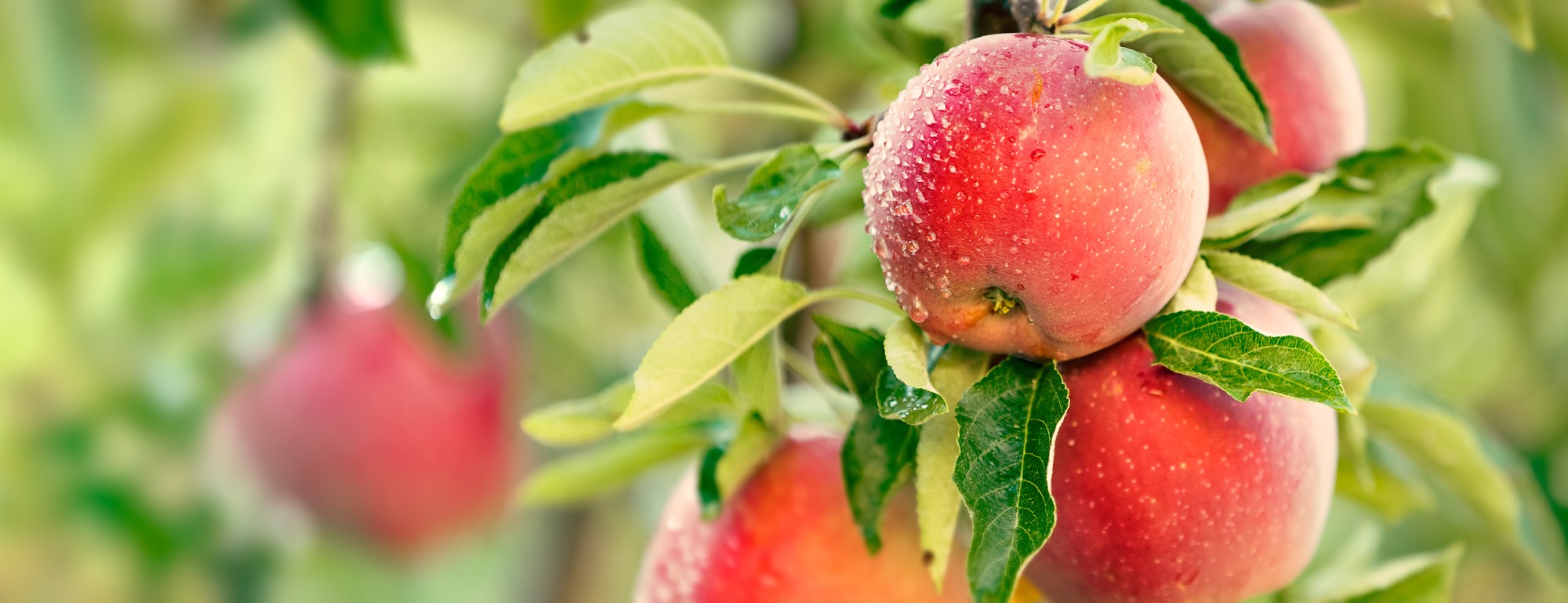
12.03.2024
Very juicy!
The tasty fruit juices under the “beckers bester“ name are well-known in Germany. The family-owned business, currently run by the third generation, has for the last 75 years been based in Lütgenrode in the south of the Lower Saxony region. HYDRAULIKPRESSE took a look behind the scenes at this long-standing business.
Freshly squeezed fruit juice nowadays comes in convenient bottle or carton form. That wasn‘t always the case. It was as late as 1932 that company founder Bertha Becker succeeded in making fruit juices durable, and so suitable for storing. This made her one of the groundbreakers in paving the way for today‘s high-tech, high-volume fruit juice and fruit drink production. The beckers bester business is today one of the leading fruit juice manufacturers in Germany.
The name beckers is still closely associated with apple juice, which was the company‘s original product. Even though the beckers bester/NEU’s business now offers a range of some 70 different flavours, and its in-house product development department is continually searching for contemporary solutions, such as the new health-enhancing soya-based fruit drinks, apple juice remains the “elixir of life“.
In earlier times production used to run day and night from the start of the apple harvest in September through to December. Fruit processing was a seasonal operation. That has now changed.
400 football pitches full of apple trees
Following the reforms in the former East Germany, beckers established contacts with the state-owned fruit juice corporation in Eisleben, the birthplace of Martin Luther, and in 1993, after German reunification, constructed a state-of-the-art press house in the town. Even while the harvest is still in progress, apples are being turned into juice in Eisleben, as well as being placed in storage, so processing is able to continue all the way through until May of the following year. The Eisleben facility presses as many as 60,000 tonnes of apples into apple juice every year. Over an area of 300 hectares – that‘s about 400 football pitches – in the Thuringia and Saxony regions of Germany, contract growers grow some 180,000 apple trees whose fruit is processed into apple juice in Eisleben.
Together with other self-pressed juices such as blackcurrant, cherry and strawberry, a total of 35 million litres of juice is held in storage in gigantic stainless steel tanks in Eisleben. From there the juice is transported by tanker to the bottling and packing plants in Lütgenrode and Freinsheim. There the juice is poured into environmentally reusable or disposable glass bottles, PET bottles and Tetra-pak cartons, as well as reusable plastic bottles. It is not only in terms of its natural product that beckers places great value in environmental awareness. Its entire production process is environmentally optimised: from its in-house sewage treatment plant, to its energy-saving method of heat recovery.
At the headquarters in Lütgenrode juices are bottled or packed and also processed into other drinks. Tanks hold 15 million litres of permanent stocks of fruit juice and fruit juice-based drinks in order to be able to respond to customer enquiries at all times. The juices and juice concentrates stored here are procured by beckers from all over the world, so as to provide consumers with a broad choice of different juices: tomatoes and Williams pears from Italy, orange juice from Brazil, pineapple from Indonesia and guava from Malaysia. A complex three-shift production system is operated, with the products being stored in a high-shelf warehouse with capacity for 11,500 pallets.
Pipes and hoses
At the bottling/packing plant in Lütgenrode all connections are executed as piping wherever possible, but in a facility of such a kind there is always something which also needs to be pumped through flexible hose lines. The tanks containing the semi-concentrates are filled with nitrogen, for example, to prevent air from penetrating into them, because oxygen in the air leads to oxidation, which may result in the entire batch being lost. To feed the nitrogen – the so-called inert gas – into the tank, mobile distribution stations with metal hoses are used. In this way, the semi-concentrates can be stored for a year at a temperature of 10°C; the fully concentrated juices are preserved by the fructose.
The flexible hose lines from HANSA‑FLEX are also deployed in pumping the juices around to the various production stages. They are also used for unloading the tankers, from which the juice is pumped via flexible PTFE hoses into the storage tanks. Before the tanks are filled with fruit juice, they are treated with steam in order to sterilise them. And in the production environment, too, HANSA‑FLEX PTFE hoses are popular, because they are much lighter and more flexible than the hoses previously used.
PTFE hoses also have other natural properties which were decisive in the decision by Olaf Brakmann, plant manager in Lütgenrode, to choose the HANSA‑FLEX product. With FDA approval, they are approved for use in the food and drinks industry, and are neutral in odour and taste. They also provide bacteriological safety, thereby ensuring the juices have a long shelf life. The hose lines must have no creases or bubbles in which juice residues might collect during cleaning and subsequently cause problems in terms of microbiological contamination. PTFE hoses offer a high degree of safety in that respect, and prevent such problems from occurring. They are also durable, and so reduce operating costs.
Olaf Brakmann indicates another key aspect: the high pressure absorption of the PTFE hoses. This is important because orange juice concentrate, for example, is pumped at pressures of up to 15 bar through the piping and hose systems. This high pressure is necessary because the concentrate is very viscous. A special fitting on the hoses supplied for many years by HANSA‑FLEX Boffzen prevents static charging. The beckers bottling/packing plant has many hose lines in operation, and so is able to provide its own back-up if a sudden failure occurs, but nevertheless HANSA‑FLEX Boffzen guarantees continuous replacement of all hoses. So that “beckers bester“ remains the best.
Learn more
- 12.03.2024
A real challenge
HANSA-FLEX is a Zeppelin service partner for Cat construction machinery and enginesFind out more - 11.03.2024
Clean oil, clean cement production
How Holcim turns a by-product of pig iron production into a valuable raw material for cement production, and why clean hydraulic oil is indispensable.Find out more