Avec sa plate-forme mobile Quadriga, le groupe M révolutionne l’entretien des briques dans les fours industriels : un robot télécommandé équipé d’un marteau hydraulique effectue des travaux de réparation auparavant manuels de manière plus sûre et plus rentable.
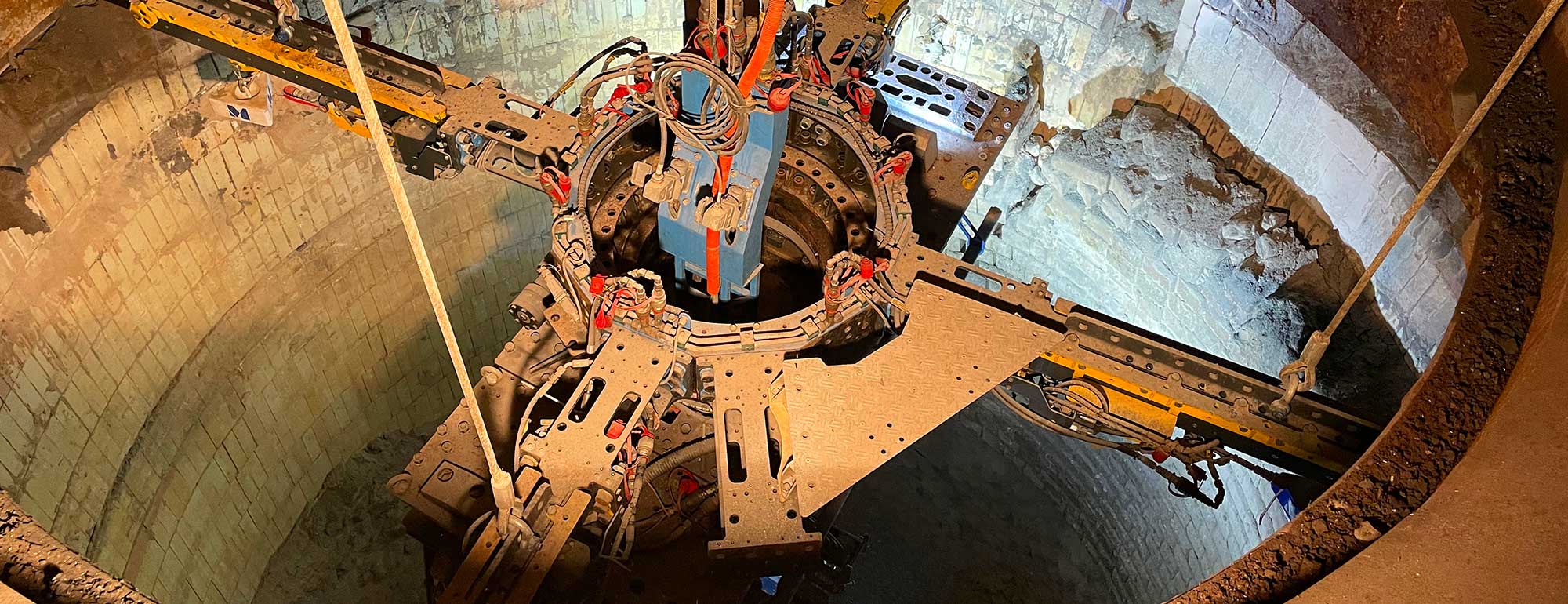
12.03.2024
Une révolution numérique dans les opérations industrielles
La maçonnerie des fours industriels doit être réparée régulièrement. Avec sa plate-forme mobile Quadriga, unique au monde, le groupe M a réussi pour la première fois à combiner les objectifs concurrents que sont la sécurité au travail, le gain de temps, la réduction des coûts et l’optimisation des processus.
Aussi différents que le ciment, l’acier, le verre, l’aluminium ou même le sucre puissent paraître à première vue, ils ont un facteur central en commun : les fours industriels sont indispensables à leur production. Les températures dépassant largement les 1 000 °C sont monnaie courante. Par exemple, une température de 1450 °C est nécessaire pour brûler du ciment. Les fours sont revêtus à l’intérieur de briques réfractaires afin d’optimiser l’efficacité de la chaleur. Les sections revêtues de briques atteignent des diamètres de 15 mètres et des hauteurs de 100 mètres.
Les inspections et révisions régulières des fours industriels et surtout de leur maçonnerie sont obligatoires : “Lors de la production de ciment, l’abrasion provoque l’érosion du revêtement ignifuge. À cela s’ajoutent les contraintes liées aux changements de température et à la corrosion thermochimique, qui entraînent l’endommagement et l’écaillage de la maçonnerie”, explique Bennet Röpke, chef de projet chargé du développement du Quadriga au sein du M-Group. Pour entretenir la maçonnerie, les opérateurs de l’usine ou les prestataires de services spécialisés devaient auparavant monter un échafaudage à l’intérieur du four. Les dépôts étaient ensuite retirés de la surface de la maçonnerie et les briques endommagées étaient enlevées et remplacées. Il s’agit d’un travail physiquement exigeant qui n’est pas sans danger pour les maçons spécialisés en raison de la mauvaise visibilité, des températures élevées, des chutes de briques, de la poussière et du bruit. Il prend également beaucoup de temps et est très coûteux. Dans une cimenterie, les coûts d’immobilisation peuvent rapidement atteindre 200 000 euros par jour. La coordination des différents corps de métier impliqués est un autre facteur d’incertitude.
La révolution au lieu de l’évolution
Karen Maria Mönstermann, de la section des relations publiques et du marketing de l’entreprise, décrit la pression qui sous-tend ce nouveau développement : “Il n’y a eu pratiquement aucun progrès dans ce domaine au cours des cent dernières années. Nous avons donc cherché une solution permettant d’optimiser simultanément les facteurs diamétralement opposés que sont la sécurité au travail, les coûts, le temps et la qualité du processus”. Avec le Quadriga, le M-Group a développé une solution qui n’est pas une simple évolution, mais une véritable révolution dans la maintenance des fours industriels. L’échafaudage précédemment utilisé est remplacé par une plate-forme qui se déplace verticalement de haut en bas à l’intérieur du four grâce à des câbles. Jusqu’à six vérins hydrauliques soutiennent solidement les côtés de la plate-forme. Le gain de temps par rapport aux échafaudages traditionnels est énorme : alors que le montage et le démontage dans un four prenaient environ 100 heures, la plate-forme ne prend que 14 heures pour le même usage.
Opérations numérisées
Cependant, l’innovation ne se limite pas au remplacement de l’échafaudage. Avec le Quadriga, un bras robotisé qui peut pivoter et tourner dans toutes les directions avec un marteau à commande hydraulique effectue le travail de démolition de la maçonnerie qui était auparavant manuel. L’avantage est que le pilote de Quadriga, qui contrôle le bras robotisé, se trouve à l’extérieur du four dans une cabine qui sert de centre de contrôle. Plusieurs caméras, microphones et capteurs maintiennent le contact entre le four et le centre de contrôle. “La numérisation des travaux de maintenance avec la plateforme Quadriga augmente non seulement la sécurité au travail, mais aussi l’efficacité, car le bras robotisé peut être utilisé 24 heures sur 24 et 7 jours sur 7. En même temps, nous soulageons nos employés et rendons notre métier plus attrayant pour les jeunes”, déclare Mme Mönstermann, résumant les avantages offerts par Quadriga.
Hydraulique décentralisée
Pour protéger le groupe hydraulique des vibrations et de la poussière, il est situé à l’extérieur du four pour en faciliter l’entretien. Les lignes d’alimentation et de retour sont reliées à la plate-forme Quadriga par un triple enrouleur de tuyau d’une longueur de 40 mètres. Le troisième tuyau transporte de l’air comprimé pour le nettoyage des caméras, mais il peut également être utilisé pour le système hydraulique en cas de problème. “Pour l’enrouleur, nous utilisons les tuyaux Pro de HANSA-FLEX, qui sont beaucoup plus résistants à l’abrasion que les tuyaux standard grâce à leur revêtement en plastique durci”, explique M. Röpke.
Nous formulons nos exigences et HANSA-FLEX nous fait rapidement des propositions parmi lesquelles nous pouvons choisir. Le développement s’en trouve facilité et nous recevons en même temps des informations précieuses.
Bennet Röpke
Chef de projet du Quadrige
Service personnalisé
Un grand nombre de composants HANSA-FLEX sont utilisés dans la plate-forme Quadriga. Les espaces d’installation restreints exigent parfois des solutions créatives en matière d’hydraulique, notamment parce que le Quadriga doit être transporté de manière peu encombrante, ce qui se traduit par des espaces d’installation restreints. M. Röpke apprécie la proximité de la succursale de Lemgo et le contact personnel : “Nous spécifions nos besoins et HANSA-FLEX nous fait rapidement des propositions parmi lesquelles nous pouvons choisir. Cela facilite notre travail de développement, tout en nous apportant des idées précieuses.” Andre Dux, Account Manager chez HANSA-FLEX, est le point de contact central pour la coordination entre la succursale, le Rapid Hydraulic Service, la production de vérins, l’ingénierie et la construction de groupes électrogènes ainsi que la filiale de HANSA-FLEX, Willmann Steuerungstechnik. “Nous sommes fiers de soutenir un développement aussi novateur et de pouvoir apporter notre expertise dans les domaines les plus divers de l’hydraulique”, déclare M. Dux.
En savoir plus
- 12.03.2024
Partenaires égaux
Avec plus de 125 ans d'expérience dans les machines de compactage et un travail de pionnier dans le domaine de la technologie d'oscillation, Hamm est l'un des leaders de la branche. Il est donc logique que le spécialiste de la technologie de compactage collabore avec HANSA-FLEX.En savoir plus - 12.03.2024
Parfaitement soignées
Les amateurs de sports d'hiver attendent des pistes parfaitement damées, qu'il s'agisse d'une descente rapide, d'un carving élégant, de ski de fond classique ou de skating, ou de figures époustouflantes avec un snowboard dans le fun park ou en hors-piste. Pour le damage de leurs pistes et de leurs parcs à neige, les stations de…En savoir plus - 12.03.2024
Gestion efficace des tuyaux
Sur le site de GKN à Kaiserslautern, environ 400 employés produisent des arbres d'hélice avec des joints homocinétiques sur une surface de plus de 20 000 m². La plupart des machines automatisées de traitement des pièces sont à entraînement hydraulique, y compris les systèmes de meulage, de tournage et de fraisage. GKN utilise également l'hydraulique…En savoir plus